New 3D printing technology is rapidly transforming manufacturing, design, and various industries. From the familiar FDM and SLA methods to groundbreaking innovations like bioprinting and 4D printing, the possibilities are vast. This technology is enabling the creation of complex, customized parts with unprecedented precision and speed, impacting everything from aerospace to medical applications.
This exploration delves into the evolution of 3D printing, highlighting emerging trends, material advancements, and the profound impact on manufacturing processes. We’ll analyze the strengths and weaknesses of different techniques, examining how they’re pushing the boundaries of design and production.
Introduction to 3D Printing Technologies
D printing, also known as additive manufacturing, has revolutionized various industries by enabling the creation of complex three-dimensional objects from digital designs. This technology encompasses a wide range of methods, each with its own strengths and weaknesses, making it suitable for diverse applications. From prototyping to manufacturing, 3D printing offers unparalleled flexibility and efficiency.
Existing 3D Printing Methods
Various 3D printing techniques exist, each employing unique principles and materials. Familiar examples include Fused Deposition Modeling (FDM), Stereolithography (SLA), and Selective Laser Sintering (SLS). Understanding these methods and their characteristics is crucial for selecting the appropriate technology for a specific task.
- Fused Deposition Modeling (FDM) is a widely used method that extrudes molten thermoplastic material layer by layer to build up a three-dimensional object. This process is relatively inexpensive and accessible, making it popular for prototyping and low-volume production.
- Stereolithography (SLA) utilizes a vat of liquid resin that is cured by a UV laser. The laser selectively hardens the resin, creating each layer of the object. SLA produces highly detailed parts and is often preferred for intricate designs.
- Selective Laser Sintering (SLS) employs a high-powered laser to selectively sinter powdered materials, such as nylon or metal powders. This process enables the creation of complex geometries and functional parts.
Fundamental Principles of 3D Printing
At its core, 3D printing involves the layer-by-layer construction of three-dimensional objects. Digital models, often created using computer-aided design (CAD) software, are sliced into thin layers. The 3D printer then deposits material, according to the instructions in the digital design, to form the desired object. This additive process contrasts with traditional subtractive manufacturing methods, which remove material from a block of material.
Types of Materials Used in 3D Printing
A diverse range of materials are employed in 3D printing, each possessing unique properties and characteristics. The selection of materials is crucial for achieving the desired performance and functionality of the final product.
- Thermoplastics, such as ABS and PLA, are commonly used in FDM due to their relatively low cost and ease of processing. Their thermoplastic nature allows for repeated heating and cooling, enabling flexibility in the printing process.
- Resins are commonly used in SLA, offering high precision and detail. These resins can be cured using UV or other light sources, enabling intricate structures.
- Metal powders are used in SLS for creating strong and durable parts. The selective sintering process allows for the creation of complex geometries with high precision and strength.
Comparison of 3D Printing Technologies
The following table provides a comparative analysis of the strengths and weaknesses of different 3D printing technologies.
Technology | Material Capabilities | Speed | Cost | Resolution |
---|---|---|---|---|
FDM | Thermoplastics | High | Low | Medium |
SLA | Resins | Medium | Medium | High |
SLS | Metal powders, polymers | Medium | High | High |
Emerging Trends in 3D Printing
D printing, once a niche technology, is rapidly evolving, driven by advancements in materials science and engineering. This evolution is creating new possibilities in various sectors, from healthcare to manufacturing. This section explores some of the emerging trends, highlighting their potential applications and characteristics.
Bioprinting
Bioprinting is a specialized 3D printing technique that uses biological materials, such as cells and tissues, to create functional biological structures. This technology holds significant promise for regenerative medicine and tissue engineering. The process involves depositing biological materials layer by layer, guided by computer-aided design (CAD) models, to form complex structures. Successful bioprinting relies on precise control over the deposition process, material properties, and cell viability.
- Potential Applications: Bioprinting can create functional tissues for transplantation, such as cartilage, bone, and skin. It can also be used to fabricate organoids, which are miniaturized versions of organs, for drug testing and research.
- Advantages: Bioprinting allows for the creation of customized tissues and organs tailored to individual patient needs, potentially reducing the need for organ donors and improving patient outcomes.
- Disadvantages: Current bioprinting technologies face challenges in maintaining cell viability during the printing process and ensuring long-term functionality of the printed tissues.
4D Printing
D printing, a burgeoning field, extends 3D printing by incorporating time as a design parameter. These printed objects are capable of changing shape or form in response to external stimuli, such as temperature, light, or moisture. This ability enables the creation of complex, adaptive structures with potentially revolutionary applications.
- Potential Applications: 4D-printed structures can be designed to respond to specific environmental cues, such as self-folding for intricate packaging, transforming from one structure to another based on external triggers, or adjusting their shape for enhanced functionality in various fields.
- Advantages: 4D printing allows for the creation of dynamic and adaptive structures, opening up new possibilities for engineering and design. The adaptive nature of these structures could lead to significant improvements in fields like aerospace, architecture, and medicine.
- Disadvantages: The complexity of designing and controlling the temporal properties of 4D-printed structures poses a significant challenge. The long-term stability and reliability of these structures also need to be thoroughly investigated.
Binder Jetting
Binder jetting is a 3D printing technique that uses a binder to bond powder materials together. It offers a balance between speed and material versatility. Powder materials, such as metal, ceramic, or polymer, are selectively bonded by a binder jet, forming a three-dimensional object.
- Potential Applications: Binder jetting has demonstrated success in manufacturing complex parts with intricate geometries, and it’s particularly attractive for large-scale production of metal parts.
- Advantages: Binder jetting is cost-effective compared to other 3D printing techniques. It can handle a wide range of materials, opening up possibilities for diverse applications.
- Disadvantages: The accuracy and surface finish of the printed parts can be affected by the binder jetting process. Post-processing steps may be required to achieve the desired quality.
Summary Table
Technology | Key Characteristics | Applications | Advantages | Disadvantages |
---|---|---|---|---|
Bioprinting | Uses biological materials to create tissues and organs. | Regenerative medicine, tissue engineering, drug testing. | Customized tissues, potential reduction in organ donation need. | Maintaining cell viability, long-term functionality. |
4D Printing | Incorporates time as a design parameter, creating adaptive structures. | Adaptive structures, self-folding, responsive systems. | Dynamic, responsive structures, enhanced functionality. | Complexity of design, long-term stability. |
Binder Jetting | Bonds powder materials with a binder jet. | Complex parts, large-scale production of metal parts. | Cost-effective, wide material range. | Accuracy, surface finish, post-processing requirements. |
Materials Advancements: New 3d Printing Technology
D printing technology is rapidly evolving, driven in part by advancements in the materials used in the process. This evolution is crucial, as the properties of these materials directly influence the design possibilities and applications of 3D-printed objects. New materials offer exciting opportunities for creating stronger, lighter, and more specialized parts.Exploring new materials allows for the design of objects with enhanced functionalities, tailored to specific needs.
From biocompatible polymers for medical implants to advanced composites for aerospace applications, the possibilities are expanding rapidly. This shift towards novel materials also significantly impacts the design space for 3D printing, opening up new avenues for creative problem-solving and innovation.
Biocompatible Materials
Biocompatible materials are crucial for applications in the medical field, where implants and prosthetics must integrate seamlessly with the human body. These materials are designed to minimize adverse reactions and promote healing. A key characteristic of biocompatible materials is their ability to interact favorably with biological systems. Polymers like polylactic acid (PLA) and polycaprolactone (PCL) are frequently used for their biodegradability and biocompatibility.
- Polymers like PLA and PCL exhibit good biocompatibility, promoting tissue integration and minimizing rejection risks.
- They can be tailored for specific applications by altering their mechanical properties through additives and processing parameters.
- Successful applications include creating custom bone implants and scaffolds for tissue regeneration, enabling precise structural design and controlled drug delivery.
Composite Materials
Composite materials combine two or more distinct materials to create a new material with enhanced properties. This approach allows for the integration of different material strengths, creating products with unique functionalities. For instance, a composite material might combine the strength of a metal with the lightness of a polymer.
- The properties of composites are often superior to those of the individual components, leading to more robust and versatile parts.
- Examples include carbon fiber-reinforced polymers, which are used in aerospace and automotive applications for their high strength-to-weight ratio.
- The combination of materials allows for greater design flexibility, enabling the creation of components with tailored mechanical and thermal properties.
Metal Alloys
Metal alloys, particularly in the form of powders, are increasingly employed in 3D printing due to their potential for producing intricate designs and complex geometries. The powder-based approach, using selective laser melting (SLM), offers greater control over material deposition and part properties.
- Metal alloys, especially when used in SLM, allow for precise control of microstructure and properties, influencing the final mechanical characteristics.
- This precision leads to improved mechanical properties like strength and hardness in the printed parts.
- The use of metal alloys in 3D printing enables the creation of complex, high-performance parts, including those in aerospace and automotive industries.
Technological Innovations in Printing Processes
Three-dimensional printing, or additive manufacturing, has experienced remarkable advancements in recent years, driven by innovations in printing processes. These improvements have led to significant increases in resolution, speed, and accuracy, impacting the production of intricate and complex 3D printed parts. This evolution is shaping the future of manufacturing across diverse industries.
Advancements in Printing Resolution
Improvements in resolution allow for finer details and intricate geometries to be captured in 3D printed parts. Laser-based technologies, such as selective laser melting (SLM) and laser engineered net shaping (LENS), are key drivers in achieving high-resolution structures. These technologies use highly focused laser beams to precisely melt or fuse materials layer by layer, resulting in extremely fine details and high precision.
Advances in materials science also contribute to improved resolution, as enhanced material properties facilitate the creation of more refined structures. For example, the development of specialized polymers with superior dimensional stability and lower shrinkage rates directly enhances the resolution capabilities of processes like fused deposition modeling (FDM).
Accelerated Printing Speeds
The speed at which 3D printing processes operate is crucial for efficient production. Advances in printing mechanisms and software algorithms play a pivotal role in increasing speed. Optimized software controls the movement of print heads and the distribution of materials, reducing idle time and enabling faster layer deposition. Simultaneous multi-extrusion and multi-laser systems are examples of advancements that have led to significant increases in printing speeds.
These advancements have made 3D printing a viable option for rapid prototyping and short-run production. For instance, the production of custom-fit medical implants and intricate aerospace components is accelerated due to enhanced printing speeds.
Enhanced Printing Accuracy
Accuracy in 3D printing is vital for ensuring the dimensional precision of manufactured parts. Advanced control systems and feedback mechanisms, combined with precision sensors, have led to remarkable accuracy improvements. These systems constantly monitor and adjust the printing process, reducing errors and variations in part dimensions. Software improvements also contribute to accuracy by refining the design models and optimizing the printing parameters for specific materials.
These improvements have enabled 3D printing to meet the stringent requirements of industries like aerospace and medical technology, where precise tolerances are critical.
Evolution of Printing Processes
The table below illustrates the evolution of 3D printing processes over time, highlighting improvements in resolution, speed, and accuracy. These advancements reflect the continuous pursuit of greater efficiency and precision in additive manufacturing.
Time Period | Technology | Resolution (µm) | Speed (mm³/hr) | Accuracy (µm) |
---|---|---|---|---|
2000-2010 | Early FDM, SLA | 50-100 | 1-10 | 20-50 |
2010-2020 | SLM, SLS, Selective Laser Sintering | 20-50 | 10-100 | 10-20 |
2020-present | Multi-material, hybrid, high-resolution FDM, bioprinting | 10-2 | 100-1000+ | 5-2 |
Applications of New 3D Printing Technology
New 3D printing technologies are rapidly expanding their reach across diverse industries, offering unprecedented possibilities for design, manufacturing, and innovation. From aerospace to medicine, and beyond, these technologies are revolutionizing how products are conceived and produced, leading to lighter, stronger, and more customized solutions. This section explores the key applications, highlighting specific examples, and analyzing the challenges and opportunities associated with each.
Aerospace Applications
Advanced 3D printing methods, particularly those utilizing metal alloys, are transforming the aerospace industry. These technologies enable the creation of intricate, lightweight components with complex geometries previously unattainable through traditional manufacturing processes. The result is improved fuel efficiency, reduced weight, and enhanced performance in aircraft.
- Engine components: 3D-printed engine parts, such as turbine blades and compressor housings, can be designed for optimized airflow and reduced weight, leading to significant gains in fuel efficiency. Examples include the use of titanium alloys for improved strength and heat resistance. This results in lighter aircraft with potentially lower operating costs.
- Aircraft structures: 3D printing enables the creation of customized, lightweight structures, leading to improved performance and reduced fuel consumption. For example, 3D-printed panels and spars can reduce the overall weight of the aircraft, potentially increasing the payload capacity and range.
The opportunities in this sector are substantial. However, challenges remain, such as ensuring the reliability and durability of 3D-printed components under extreme conditions. Certification processes for 3D-printed parts in aerospace applications need further development.
Medical Applications
D printing is revolutionizing healthcare by enabling the creation of personalized medical devices and implants. The ability to design customized solutions tailored to individual patient needs is a significant advantage.
- Prosthetics and implants: 3D-printed prosthetics and implants can be precisely customized to fit the unique anatomy of each patient, leading to improved comfort, functionality, and integration with the body. Biocompatible materials are critical for long-term success in this application.
- Surgical guides and tools: 3D-printed surgical guides and tools can enhance surgical precision and reduce invasiveness. These guides allow for more accurate positioning and alignment during procedures, potentially leading to better patient outcomes.
- Drug delivery systems: 3D printing allows for the creation of complex drug delivery systems tailored to individual patient needs. This can enhance drug efficacy and reduce side effects.
The potential for improved patient outcomes and reduced costs is substantial. However, the need for rigorous testing and validation of 3D-printed medical devices to ensure safety and efficacy remains a key challenge.
Automotive Applications
D printing is also making its mark in the automotive industry. It’s being used to produce functional prototypes and customized parts, enabling rapid design iterations and cost savings.
- Interior and exterior components: 3D-printed components such as dashboards, seats, and even exterior parts can be customized to meet specific design requirements. This allows for the rapid prototyping of new designs and potentially lower production costs for high-volume parts.
- Functional prototypes: 3D printing enables the creation of complex prototypes rapidly and affordably. This allows engineers to test different designs and configurations more efficiently, reducing the time and cost of development cycles.
- Specialized tooling: 3D-printed tooling can be customized for specific applications, increasing the efficiency of manufacturing processes. This is especially useful for high-volume, low-cost manufacturing.
The ability to create customized and complex parts quickly and cost-effectively presents significant opportunities. However, concerns regarding the durability and reliability of 3D-printed components under the stresses of automotive applications are present. Furthermore, standardization and certification processes for 3D-printed automotive parts are still under development.
Potential Impact on Industries
Design Considerations for New 3D Printing Technologies
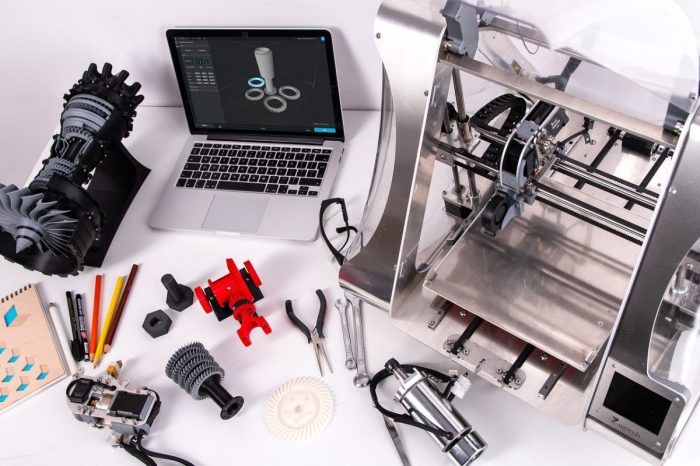
Designing for 3D printing is fundamentally different from traditional manufacturing. The inherent capabilities and limitations of various 3D printing technologies significantly impact the design process. Understanding these impacts is crucial for creating functional, efficient, and cost-effective products. Effective design strategies leverage the strengths of these technologies to optimize the entire product lifecycle.Product designs must adapt to the capabilities of new 3D printing technologies.
This involves considering factors like material properties, layer resolution, build volume, and support structures. Designing with 3D printing in mind requires a shift in mindset, moving away from traditional constraints and embracing the possibilities offered by these emerging technologies.
Impact on Product Design
The shift towards 3D printing necessitates a change in the traditional product design approach. The ability to fabricate complex geometries directly from a digital model opens new possibilities for product innovation. This includes the potential for intricate internal structures, customized designs, and optimized functionality.
Adapting Designs to New Technologies
Designs must adapt to the inherent limitations of each 3D printing technology. For instance, FDM (Fused Deposition Modeling) prints with thermoplastic filaments, limiting material choices and potentially impacting the final product’s strength and durability. SLA (Stereolithography) designs are constrained by the resin’s viscosity and curing process. Bioprinting designs need to consider cell viability and the intricate nature of biological tissues.
Design Strategies Leveraging Strengths
Strategic design considerations are critical for realizing the full potential of 3D printing technologies. Designing for support structures, optimizing part orientation for efficient printing, and understanding material properties are crucial steps.
Example Design Strategies
- FDM (Fused Deposition Modeling): Designs for FDM should prioritize simple geometries and minimize overhangs. Support structures are often necessary for complex shapes. Consider using a modular design approach, allowing for easier assembly and repair.
Example design 1 (FDM): A lightweight, interlocking toy component featuring a series of simple, interlocking geometries designed to minimize support structures and maximize print efficiency. The design incorporates a well-defined base for optimal support during the printing process.
- SLA (Stereolithography): Designs for SLA should focus on intricate details and complex shapes. The high resolution of SLA allows for detailed features that might be difficult to achieve through other methods. The design should incorporate a strategy to reduce the need for support structures.
Example design 2 (SLA): A highly detailed medical model featuring intricate vascular structures and internal organs. The design takes advantage of SLA’s precision to accurately represent the anatomical features, minimizing the need for additional post-processing steps.
- Bioprinting: Designs for bioprinting need to consider cell viability and the unique properties of biological materials. The design should incorporate factors such as cell seeding patterns and material properties. Designs need to prioritize scalability for future applications.
Example design 3 (Bioprinting): A scaffold for tissue engineering, featuring a porous structure optimized for cell growth and tissue regeneration. The design takes into account the specific biomaterial used, ensuring optimal cell adhesion and proliferation.
Manufacturing Processes with New 3D Printing
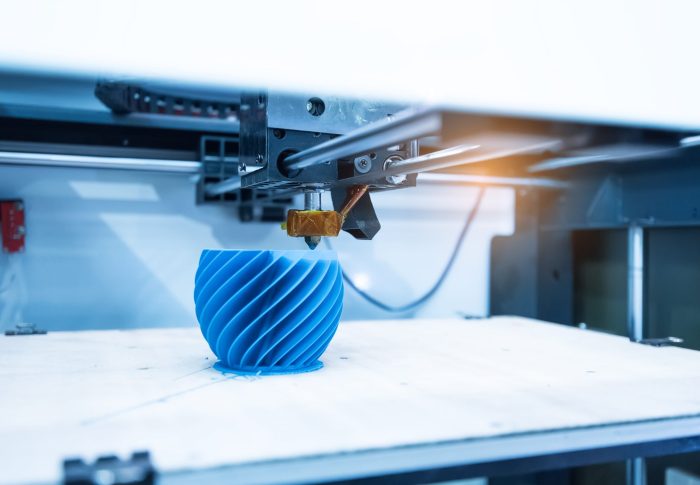
New 3D printing technologies are revolutionizing manufacturing processes, offering unprecedented flexibility and potential for customized solutions. These technologies enable the creation of complex geometries and intricate parts previously unattainable through traditional methods, leading to significant improvements in efficiency and cost reduction. The adaptable nature of 3D printing allows for on-demand production, minimizing material waste and reducing lead times.
Direct Energy Deposition (DED)
DED processes leverage concentrated energy sources to melt and deposit material layer by layer. This method is particularly well-suited for creating large, complex components with intricate internal structures. The workflow typically involves carefully controlling the energy source and feed rate to ensure consistent deposition and desired geometry. The use of DED is prevalent in aerospace and industrial applications, where high strength-to-weight ratios are critical.
Selective Laser Sintering (SLS)
Selective Laser Sintering (SLS) is a powder-bed fusion process that uses a laser to selectively melt and fuse powdered material. The process involves a precise scanning pattern to build up the desired component layer by layer. The process excels in producing intricate parts with high precision.
Stereolithography (SLA)
Stereolithography (SLA) is a vat-based process that uses a laser to cure liquid resin into a solid shape. The workflow involves precisely controlling the laser’s trajectory to build the component layer by layer. This method is commonly used for producing highly detailed parts with smooth surfaces.
Material Properties and Design Considerations
The choice of 3D printing method significantly influences the final properties of the manufactured product. Factors such as material compatibility, part geometry, and desired mechanical properties need careful consideration. Design considerations for 3D printed parts often differ from traditional designs, emphasizing features that leverage the inherent capabilities of the printing process.
Impact on Supply Chains
New 3D printing technologies can significantly affect supply chains by enabling localized production. This localized manufacturing approach reduces reliance on centralized suppliers, potentially lowering transportation costs and lead times. 3D printing allows for faster adaptation to changing demands and customized product designs. The ability to produce parts on-demand reduces inventory costs and allows for more agile responses to market fluctuations.
Examples of Efficiency and Cost Reduction
D printing enables the creation of complex, lightweight parts, leading to weight savings in industries like aerospace and automotive. This directly translates to fuel efficiency gains and reduced material costs. The localized production capability of 3D printing allows companies to reduce reliance on global supply chains, which can lead to cost savings in logistics and transportation. On-demand production also minimizes material waste, as only the necessary material is used.
The reduction in lead times can drastically reduce project completion times and increase overall profitability.
Societal Impact of New 3D Printing Technologies
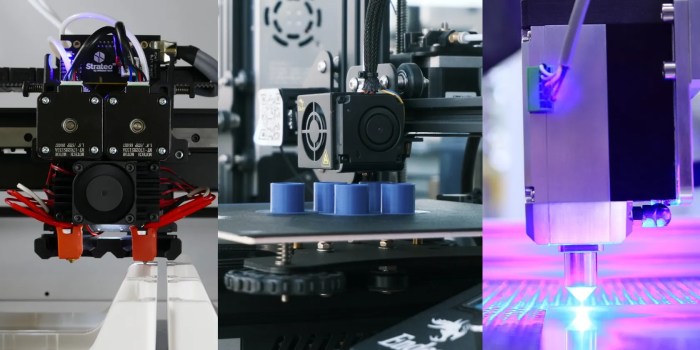
New 3D printing technologies are poised to revolutionize various aspects of society, from manufacturing and healthcare to daily life. This transformative potential brings with it a complex interplay of opportunities and challenges, impacting accessibility, affordability, the environment, and the future of work. Understanding these implications is crucial for harnessing the benefits of these technologies responsibly.
Accessibility and Affordability
The democratization of manufacturing through 3D printing has the potential to significantly impact accessibility. Small businesses and individuals can potentially produce customized products without the high costs and long lead times associated with traditional manufacturing. This could lead to increased competition and innovation, while also enabling access to essential goods in remote or underserved areas. However, the initial cost of 3D printing equipment can still be prohibitive for many, creating a barrier to entry for some.
The development of more affordable, user-friendly 3D printers, coupled with the proliferation of shared or community-based printing facilities, could address this issue.
Environmental Considerations
The environmental impact of 3D printing is a significant area of concern. The materials used in 3D printing, their sourcing, and the energy consumption of the printing process all contribute to the overall environmental footprint. However, advancements in sustainable materials, such as bio-based polymers and recycled plastics, along with more energy-efficient printing technologies, offer promising avenues for reducing the environmental impact.
Optimizing material usage and waste management practices are critical aspects to consider.
Ethical Implications
The use of 3D printing raises several ethical concerns. Issues such as intellectual property rights, the potential for misuse of technology for illicit activities, and the creation of counterfeit products require careful consideration. Furthermore, the implications of using 3D printing for personalized medicine, such as creating custom prosthetics or organs, necessitate thoughtful ethical frameworks and regulatory oversight to ensure responsible development and deployment.
Impact on the Future of Work and Industry
D printing is expected to reshape various industries by altering manufacturing processes and creating new job opportunities. Traditional manufacturing jobs may be displaced as automation increases, but new roles in design, material science, and 3D printing operations will emerge. This transition requires proactive measures to reskill and upskill the workforce to adapt to the changing landscape. The potential for decentralized manufacturing and on-demand production can also affect the global supply chain and international trade relationships.
Scenario: A Potential Societal Impact
Imagine a remote village in a developing country. A local artisan uses a readily available, low-cost 3D printer to create custom-designed tools and agricultural equipment. The tools are customized to local needs, allowing for increased efficiency and improved crop yields. This access to affordable and personalized tools enables the village to become more self-sufficient and economically viable.
The artisan also uses the 3D printer to design and create affordable prosthetic limbs for those in need, enhancing their quality of life. This scenario highlights how 3D printing can foster economic empowerment and social progress in underserved communities.
Future Trends and Predictions
The field of 3D printing is poised for significant advancements in the coming years, promising transformative impacts across diverse sectors. These developments will be driven by innovations in materials, printing processes, and design methodologies, leading to more complex, customized, and efficient production methods.The future of 3D printing is not simply an extension of current capabilities; it represents a paradigm shift, potentially revolutionizing how we create and manufacture products.
This shift will be fueled by a convergence of technological advancements, leading to applications previously unimaginable.
Material Innovation and Customization
Material science will play a crucial role in shaping the future of 3D printing. Researchers are actively exploring new materials, pushing the boundaries of existing ones, and developing novel composites. This will enable the creation of parts with enhanced properties, such as increased strength, flexibility, or thermal resistance. Examples include biocompatible polymers for tissue engineering and high-temperature alloys for aerospace components.
Moreover, the ability to precisely tailor material properties within a single 3D-printed part will become increasingly common.
Advanced Printing Processes and Architectures
Future 3D printing processes will likely involve more complex layering and integration of multiple materials. Multi-material 3D printing, with its ability to combine diverse materials in a single print, is expected to become more sophisticated and efficient. Hybrid approaches, combining additive manufacturing with subtractive techniques, will also gain traction. The development of 4D printing, which allows for parts to change shape or function over time, will represent a major leap forward, opening up possibilities in areas like adaptive structures and responsive devices.
Integration with Other Technologies
The integration of 3D printing with other technologies will be a key driver of future advancements. The combination of 3D printing with AI and machine learning algorithms can optimize design parameters, automate processes, and improve material selection. Similarly, the connection with robotics will allow for more complex and intricate printing processes, leading to higher throughput and improved accuracy.
New 3D printing technology is rapidly evolving, incorporating advancements in materials science and design software. This integration with Integrated Digital Technologies A Comprehensive Overview ( Integrated Digital Technologies A Comprehensive Overview ) is key to the broader adoption and application of these innovative printing methods. The result is a more streamlined and efficient production process for complex designs, boosting the overall potential of 3D printing across various industries.
Furthermore, the integration with digital twins will allow for better simulation and optimization of the entire manufacturing process.
Impact on Various Sectors
The impact of these advancements will be profound across multiple sectors. In healthcare, personalized medicine and organ printing will become more accessible and effective. In aerospace, lighter and stronger components will lead to more fuel-efficient aircraft. In construction, the production of customized and complex structures will become a reality, offering greater flexibility and cost-effectiveness. In consumer goods, 3D printing will likely lead to a surge in personalized and on-demand products, drastically changing supply chains.
A hypothetical example could be the production of customized prosthetic limbs, printed in a local facility with precise material properties matching the patient’s specific needs.
A Future Scenario: The Decentralized Manufacturing Hub, New 3d printing technology
Imagine a future where 3D printing technologies are ubiquitous. Local manufacturing hubs equipped with advanced 3D printers, material libraries, and AI-powered design tools become the norm. These hubs can produce customized products on demand, responding rapidly to evolving needs. Small businesses and individuals can access these technologies, fostering innovation and entrepreneurship. The process is not limited to physical products.
New 3D printing technology is rapidly evolving, offering exciting possibilities for various applications. This advancement relies heavily on robust data management, and understanding how to effectively manage the data generated by these processes is crucial. A deep dive into the intricacies of storage and data handling, like those covered in the Western Digital Technologies Driver A Comprehensive Guide , is essential for maximizing the potential of these new 3D printing techniques.
This knowledge base ensures smooth operation and optimized output for the latest 3D printing advancements.
Imagine 3D printing customized food items, personalized pharmaceuticals, and intricate architectural models all within these hubs. This decentralized approach to manufacturing would lead to reduced transportation costs, minimized waste, and faster response times to market demands.
Outcome Summary
In conclusion, new 3D printing technology is poised to revolutionize industries across the board. The advancements in materials, processes, and applications are creating exciting opportunities for innovation and efficiency. While challenges remain, the potential for personalized production, reduced costs, and improved sustainability is undeniable. The future of manufacturing and design is being reshaped by these transformative technologies.
FAQ Insights
What are the environmental considerations of 3D printing?
The environmental impact of 3D printing is a complex issue. While it can reduce material waste in some cases compared to traditional manufacturing, the energy consumption of certain processes and the disposal of materials can still be a concern. Sustainable materials and optimized printing methods are crucial for minimizing the environmental footprint.
How does 3D printing affect the future of work?
3D printing is likely to automate some manufacturing tasks, potentially impacting certain job roles. However, it also creates new opportunities in design, material science, and maintenance. The overall impact on employment will depend on how societies adapt to the changing landscape.
What are the ethical implications of bioprinting?
Bioprinting raises ethical concerns regarding the creation and use of biological tissues and organs. Issues such as access, safety, and the potential for misuse must be carefully considered as the technology advances.
What is the cost comparison between different 3D printing technologies?
The cost of 3D printing varies significantly depending on the technology used. FDM is generally the most affordable, while SLA and SLS are often more expensive but offer higher precision and material capabilities. Factors such as material costs, machine maintenance, and labor also influence the overall cost.